
NEXUS ONCORE CONTROL
Nexus OnCore Control System
Nexus Controls' - Nexus OnCore†Control System, a distributed control system, is an advanced, fully configurable solution that improves asset visibility, provides built-in troubleshooting and maintenance tools, offers simplified expansion capabilities and reduces overall installation and training costs for your wind turbine control systems.
What is DCS and what can it do? The Nexus OnCore Control System helps wind turbine plant operators improve their speed and accuracy in making critical decisions about wind turbine controls when the plant fails to operate under normal conditions. Nexus OnCore HMI software offers a unified software environment with the ability to quickly and precisely make online changes to the application system logic that controls the plant’s operations. This capability optimizes the amount of time necessary to correct the situation without having to rely on the manufacturer.
For customers with legacy control systems that need more analytic capabilities, redundancy in controls, and a long-term supported platform, Nexus OnCore Control System provides a redundant architecture, an easy-to-use interface and simplified trending capabilities.
As your wind turbine control systems work to take control of wind, turning that energy into electricity, the Nexus OnCore Control System offers a great way for plant operators to reduce risk by increasing visibility into the lifecycle of their wind turbine asset, improving troubleshooting and simplifying programming. Unlike costly third-party platforms, the Nexus OnCore Control System also allows users to perform online configurations and changes. This distributed control system allows plant operators to have control.
For example, when your windmill air compressor isn't functioning at top speed and fails to connect to the wind turbine to activate the pump shaft, the OnCore Control System can help minimize downtime and get you back running at full capacity.
Nexus Controls delivers performance management software that tracks the efficiency and degradation of assets, process-oriented function blocks for software modification, and a robust software package that enables logic changes while the unit is operational.

SYSTEM FEATURES
KEY BENEFITS
Low total installation cost
High operational effectiveness
A single license for a unified software program
Ease of configuration, expansion and troubleshooting
Seamless interface
A single solution for multiple asset or unit types

SYSTEM ARCHITECTURE
Redundant I/O communication and power enables independent module replacement without a total system shutdown
Three-level system network provides real-time performance with high-speed data exchange where you need it most – between the controller and HMI. Non-critical information such as data backups is handled on a separate data highway.

SOFTWARE FEATURES
Logic configuration is completed online to avoid excess system outage or shutdown
The rich function block library allows the user to customize the application and/or the specific user-defined sequencing to adapt plant configurations, both current and future
Integrated HMI software package includes embedded historian and engineering tools. The historian can be expanded with no additional equipment, saving costs while enhancing analytical capability
Easily configured software can customize the HMI screen, reducing training time while improving the user experience

NEXUS ONCORE SIMULATION SOFTWARE
Provides operators a safe environment for training on turbine control systems
Offers a test environment to review changes before deploying in the operating plant
Supplies tools for troubleshooting and performing root cause analysis
Creates a platform for optimizing process parameters
Reduces distributed control system commissioning time for new plants

TURBO EXPANDER CONTROL
In addition to highly critical machinery such as turbines and generators, your plant may include vital turboexpanders for energy recovery. If so, we can help you effectively operate these assets with distributed control systems that merge safety with operational efficiency. The Nexus Control System can be configured to optimize a turboexpander operation
Reduces the distributed control system commissioning time for new plants
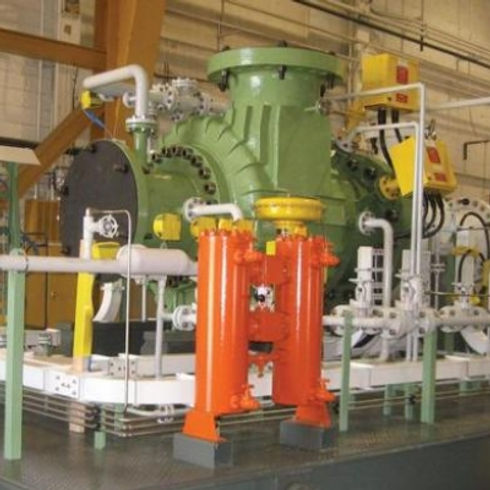